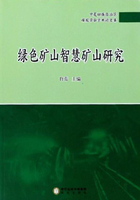
预掘双回撤通道工艺技术在枣泉煤矿大采高综采工作面的应用
邓新东
(神华宁夏煤业集团枣泉煤矿,宁夏银川750408)
摘要 神华宁夏煤业集团枣泉煤矿11采区110201大采高综采工作面采用综掘机预掘双回撤通道工艺技术代替传统的采煤机截割单回撤通道工艺技术,不仅减少了回撤通道施工工期,增加了回撤通道支护的强度、稳定性和可靠性。而且工人劳动强度明显降低,大大减少了施工安全压力,也缩短了工作面的回撤时间,并且减轻了工作面防灭火的压力,取得了较好的安全、经济和社会效益。
关键词 煤矿 大采高综采工作面 预掘双回撤通道
神华宁煤集团枣泉煤矿位于宁夏灵武市东南62 km的毛乌素沙漠的边缘,行政区划属灵武市马家滩镇管辖。井田南北长13 km,东西宽平均约4 km,面积为56.6971 km2。主采煤层为2号煤层,平均厚7.88 m,煤层倾角为3°~45°。根据煤矿特有的煤层赋存特点和地质构造,为满足高产高效综采工作面大生产的要求,2009年引进大采高综采工艺,因大采高综采工作面支架架型体积大、质量大,回撤技术研究显得尤为重要。结合110201工作面情况,采用机掘预掘双回撤通道快速回撤方法,在综采工作面停采线位置提前开掘与综采工作面平行的回撤通道与辅助回撤通道,通过2~3个回收联巷将两通道相互沟通、联络的辅巷多通道布置方式,不仅缩短了工作面的回撤时间,而且减轻了工作面防灭火的压力,实现了安全生产。
1工程概况及回采工艺
1.1工程概况
110201大采高综采工作面布置在11采区南翼第一区段的二煤煤层中,为11采区首采工作面。工作面设计走向长度2976 m,倾斜长度305 m,煤层平均厚度8.2 m,倾角6°~10°。二煤为黑色半暗型,宽条状结构,内生节理发育,矿物质含较低的低灰、低硫、低磷,是中等发热量、活性好、热稳定性好的不黏结煤。二煤顶板以厚2~4m的炭质泥岩为主,次之为砂质泥岩,局部为粉砂岩。砂质泥岩抗压强度为196~289 kg/cm2;粉砂岩抗压强度为380~399 kg/cm2。矿区北部的磁窑堡煤矿开采2层煤,顶板揭露3小时后即开始冒落。二煤底板以厚3m左右的粉砂岩、砂质泥岩为主,泥岩次之。东翼粉砂岩抗压强度为208~337 kg/cm2;西翼粉砂岩抗压强度为192~360 kg/cm2。煤尘爆炸指数为34.66%,有煤尘爆炸危险。煤的自燃倾向性一级,属于容易自燃煤层,最短自燃发火期鉴定为35天。
1.2回采工艺及设备
该工作面采用走向长壁综合机械化采煤方法进行开采,采高5.5 m,可采储量630万t。最大控顶距6.06 m,最小控顶距5.195 m,采空区顶板管理方法为全部垮落法。采煤机单向割煤,端部斜切进刀,循环进度0.865 m。工作面采用MG900/2215-GWD型双滚筒采煤机与1台SGZ1250/3×855型刮板输送机和1台 SGZ1350/525型转载机配合使用,安装184台掩护式液压支架(其中下端头3台ZYT10000/26/55D端头支架,1台ZYP10000/26/55D排头架,1台ZYGT10000/26/55D加长过渡支架,3台ZYGT10000/26/55D过渡支架,上端头4台ZYT10000/26/55D端头支架,1台ZYP10000/26/55D排头架,1台ZYGT10000/26/55D加长过渡支架,2台ZYGT10000/26/55D过渡支架),工作面有168台ZY10000/28/62D基本架。
在综采工作面回撤前的准备及回撤工作中,工作面铺网、挂钢丝绳、施工回撤通道及液压支架的回撤占用时间最多,难度最大,是工作面回撤最重要的环节。由于110201工作面沿二煤底板开采,根据工作面矿压监测数据,工作面直接顶初次垮落步距为15~17 m,初次来压步距为25~28 m,周期来压步距为20~26 m,老顶初次来压期间工作面压力较大,煤壁片帮较严重,且伪顶在支架顶梁上方破碎易脱落,周期来压工作面矿压显现不明显,但对两巷的影响较大,尤其对工作面运输巷的影响剧烈。
2原回撤通道施工方法、技术参数及支护方式
综采工作面原回撤采取单回撤通道的方式,回撤通道施工采用采煤机直接截割的方法,即回采距停采线4.0m(以大采高综采工作面回撤通道为例)时,支架停止前移,推出刮板输送机,采煤机下行割煤,及时伸出伸缩梁支护顶板。采煤机返至机窝段支架后,从下向上将工作面支架与刮板机脱开(机头、机尾各3台支架除外)。然后从下向上将工作面刮板机推至煤帮,使用采煤机再割5刀做出支架回撤通道。
回撤通道设计为矩形断面,净高度4000 mm,净宽度4000 mm。回收设备通道顶部采用锚网、W钢带联合钢梁棚子进行支护;顶板采用22#-M24-2400 BHRB400号左旋无纵筋高强度螺纹钢锚杆,锚杆间排距800 mm×900 mm,托板为150 mm×150 mm×10 mm的铁制穹形高强托板;W钢带为W280×3×3600-800-6;顶板中间布置锚索绗架,锚索间距为2.0 m,排距为2.4 m,锚索采用Φ17.8 mm×8000 mm的预应力钢绞线,锚索绗架采用11#矿工钢加工制作,加工长度2400 mm,托板为200 mm×60 mm×20 mm钢板制作。通道帮锚杆与顶板锚杆相同,锚杆间排距900 mm×900 mm,锚杆采用150 mm×150 mm×10 mm的铁制穹形高强托板配合厚度为5 mm、宽280 mm、长度为450 mm的W型钢护板使用。回撤通道内顶部使用4.4 m的“π”型钢梁一头搭在支架前梁上,搭接长度400 mm,另一头采用单体支柱支设,单体紧靠煤帮打设,打在实底上,每架支架上搭接两根“π”型钢梁,钢梁间距875 mm。
3双回撤通道施工方案、技术参数及支护方式
3.1辅助回撤通道施工方案、技术参数及支护方式
工作面回采距离停采线300~350 m时,开始自110201工作面机巷距离工作面停采线20~35 m位置预先采用机掘的方式施工辅助回撤通道,该通道作为工作面设备(工作面“三机”)撤出时的辅助运输通道,称为“辅助回撤通道”。
辅助回撤通道设计为矩形断面,掘进高度3900 mm,掘进宽度4700 mm,铺底混凝土250 mm,净高度3600 mm,净宽度4600 mm。
巷道支护采用锚网索联合支护。巷道顶部使用22#-M24-2400 BHRB500号高强左旋无纵筋螺纹钢锚杆(配套锚杆托板为150 mm×150 mm×10 mm穹形铁托板),锚杆间排距为870 mm×900 mm;帮部采用20#-M22-2000 BHRB335号左旋无纵筋螺纹钢锚杆(配套锚杆托板为150 mm×150 mm×10 mm穹形铁托板,帮部采用W280 mm×450 mm×5 mm钢护板),帮锚杆间排距为800 mm×900 mm;巷道顶部挂Φ6.5 mm圆钢焊接的钢筋网(网片规格为4600 mm×900 mm,网孔尺寸为100 mm×100 mm),帮部挂菱形金属网(网片规格为3000 mm×900 mm,网孔尺寸为50 mm×50 mm);顶部采用规格为W280×5× 4600-870-6型W钢带;巷道顶板布置锚索绗架进行支护,绗架采用11#矿用工字钢加工,长度3700 mm,锚索绗架布置三根锚索,锚索间距为1600 mm,绗架排距为1800 mm,锚索采用Φ21.98 mm×8300 mm(1×19股)的预应力钢绞线,每根锚索使用两节K2335和三节Z2370树脂药卷锚固,见图1。
图1辅助回撤通道掘进支护形式
3.2主回撤通道施工方案、技术参数及支护方式
辅助回撤通道施工完毕后,自110201工作面机巷工作面停采线位置处采用机掘的方式施工主回撤通道及其回收联络巷,该通道作为工作面液压支架回撤时的调向、装车通道,称为“主回撤通道”。
主回撤通道设计为矩形断面,掘进高度4050 mm,掘进宽度4100 mm,铺底混凝土200 mm,净高度3800 mm,净宽度4000 mm。
巷道支护采用锚网索联合支护,巷道顶部使用22#-M24-2400 BHRB500号高强左旋无纵筋螺纹钢锚杆(配套锚杆托板为150 mm×150 mm×10 mm穹形铁托板),锚杆间排距为750 mm×900 mm;北帮帮部采用20#-M22-2000 BHRB335号左旋无纵筋螺纹钢锚杆(配套锚杆托板为150 mm×150 mm×10 mm穹形铁托板,帮部采用W280 mm×450 mm×5 mm钢护板),南帮帮部采用Φ16 mm×1600 mm圆钢锚杆,帮锚杆间排距为900 mm×900 mm;巷道顶部挂Φ6.5 mm圆钢焊接的钢筋网(网片规格为4100 mm×900 mm,网孔尺寸为100 mm×100 mm),北帮帮部挂菱形金属网(网片规格为3500 mm×900 mm,网孔尺寸为50 mm×50 mm),南帮帮部挂可拉伸塑料网(网片规格为3500 mm×900 mm,网孔尺寸为40 mm×40 mm);顶部采用规格为W280×5×4600-870-6型W钢带;巷道顶板布置锚索绗架进行支护,绗架采用11#矿用工字钢加工,长度3700 mm,锚索绗架布置三根锚索,锚索间距为1600 mm,绗架排距为1800 mm,锚索采用Φ21.98 mm×8300 mm(1×19股)的预应力钢绞线,每根锚索使用两节K2335和三节Z2370树脂药卷锚固,见图2。
图2主回撤通道掘进支护形式
4双回撤通道工艺施工过程中的关键质量控制
4.1工作面开采层位及采高控制
工作面回采至主回撤通道位置时,采取采煤机直接截割的方法与之贯通,贯通质量好坏直接决定着通道支护质量及回撤空间的大小,因此,保证贯通质量是实现双回撤通道快速回撤的先决条件。
贯通的理想标准:贯通后主回撤通道顶板没有明显下沉,顶板完整;贯通后的工作面顶板基本和主回撤通道顶板一致;贯通后的工作面底板略低于主回撤通道底板,高度控制在300~600 mm之内,便于主回撤通道受工作面采动影响底鼓后起底深度的一致,最终主回撤通道打设混凝土地坪后,使工作面支架底座高度高于主回撤通道在50~100 mm之内,便于回撤支架。具体措施为:
(1)工作面铺网前预先在主回撤通道靠工作面的方向打设定位孔,间距10~20 m,定位孔距离通道底板1.5m,孔深4.0~6.0m,水平夹角与煤层走向的倾角一致,并在定位孔内充填满白灰,工作面根据定位孔位置进行贯通。
(2)在主回撤通道掘进施工过程中,详细观察巷道煤层的主要标志层层位,在工作面回采过程中以主回撤通道内的主要标志层层位来调控工作面开采层位,使之准确贯通。
(3)根据120203工作面与回收联络巷安全顺利贯通的经验,结合110201工作面煤层赋存情况,在主回撤通道内,自上而下或自下而上间隔20 m探底煤,并对其高度进行实测,绘制回撤通道素描图,在距离工作面还有20 m铺网即将贯通前,根据主回撤通道实测底煤厚度调控工作面层位,严禁上漂下挖,在此基础上严格按素描图控制好工作面开采层位及采高,使之顺利贯通。
4.2主回撤通道顶板支护控制
由于主回撤通道受工作面采动影响,产生一定的变形,为了使变形程度最小化,提前在主回撤通道顶板靠工作面方向距离帮0.5m处打设沿巷道掘进方向一致的锚索绗架进行加强支护,同时对巷道局部压力大的地段,采取架设“一梁二柱”钢梁棚子或打设单体液压点柱进行加强支护,通过采取上述措施,通道支护强度大大增加,确保了通道的畅通性,见图3、图4。
图3 110201工作面与主回撤通道贯通后效果图1
图4 110201工作面与主回撤通道贯通后效果图2
5应用分析
5.1回撤通道顶板支护安全
原采用采煤机截割施工回撤通道时,通道高度较大,人员进入煤帮作业安全性较差,锚网索支护施工困难,特别是施工第一排锚杆时,由于支架上方及支架顶梁前方距顶板已经离(脱)层,增加了施工难度,造成通道支护不及时,同时也给施工第二排锚杆带来较大的困难,整体通道支护性能较差,为此必须在支架上方挑钢梁棚子进行加强支护,才能增加人员劳动强度及安全风险。
采取机掘预掘“双回撤通道”,在预掘的巷道里,进行科学、合理、可靠的锚网索支护,局部巷道打设单体液压点柱进行加强支护,巷道受回采工作面的超前压力影响较小,综采工作面可以正常回采,直至采通为止。同时通道顶帮支护时,人员操作安全、方便,通道顶板支护及时、可靠,顶板无离(脱)层现象,通道整体支护性能好,有利于设备回收。
5.2施工时间、生产及接续、防灭火
5.2.1正常回采到停采线后采用采煤机截割做收尾空间
大采高综采工作面按照以往经验回撤综采设备,需工作面正常回采到距离停采线20 m时,开始沿工作面铺网,一直铺到工作面停采线为止。回采距停采线11 m时,开始铺设钢丝绳(Φ24.5 mm),以后每次循环铺设一根钢丝绳,共铺10根。回采距停采线4.0 m时,支架停止前移,推出刮板输送机,采煤机下行割煤,及时伸出伸缩梁支护顶板。采煤机返至机尾机窝段支架后,从下向上将工作面支架与刮板机脱开(机头、机尾各3台支架除外)。然后从下向上将工作面刮板机推至煤帮,使用采煤机再割5个循环做出净宽4.0 m和净高4.0 m的出架通道。采用此方法施工回撤通道时间为15~20 d,另外设备回撤在20~25 d,累计需要时间40~45 d,不利于工作面的安全快速回撤。
5.2.2采取机掘预掘收尾空间
在巷道布置上,先提前在综采工作面停采线处安排综掘队采取机掘预掘出“双回撤通道”,进行合理可靠的支护,因工作面回采与施工回撤通道平行作业,工作面回采至主回撤通道位置时,采取直接截割的方法与之贯通,回撤通道施工不占用额外的时间,避免了当工作面采到停采线时需做回撤空间的现象,工作面设备回撤只需20~25 d,相比提前15~20 d的准备时间,有效缓解采掘生产接续矛盾,不仅缩短了工作面的回撤时间,而且减轻了工作面防灭火的压力。
5.3工序安排
采用以往经验回撤综采设备,只有等到回撤通道施工完毕后,才可以回撤工作面运输机、采煤机、支架等,且只可以从工作面机头、机尾进行回收设备;而采用预掘收尾空间、快速回撤时,由于提前做好了回撤空间,当综采工作面采透时,由安装队及时回撤工作面运输机、采煤机、支架等,同时由于施工了3~4条回收联络巷,可以安排3~4个组多头进行作业,加快了工作面回撤速度。
5.4经济分析
采用采煤机截割施工单回撤通道技术并进行工作面设备回收的技术累计需要时间40~45 d,采用预掘收尾空间并进行工作面设备回收的技术只需20~25 d,相比提前15~20 d的时间。综采一队可提前在110203接续工作面提前组织生产30~40个小班,按平均每班割煤3刀计算,可多采出煤量275 m×5.5 m×0.865 m/循环×1.33 t/m3×(30~40)×0.95=(49591~66122)吨,间接创造产值(49591~66122)吨×260元/吨=(1289.366~1719.172)万元。
6结束语
综上所述,在缓倾斜大采高综采工作面采用机掘预掘“双回撤通道”技术回收设备,技术经济效益显著,可行性强。因此,枣泉煤矿在110201大采高综采工作面采用机掘预掘“双回撤通道”技术,不仅对提高综采工作面回撤效率和安全保障性具有技术革新意义,并为集团公司各原煤生产单位综采工作面采用机掘预掘“双回撤通道”技术实践应用积累了宝贵的实战经验。
参考文献
[1]郭胜利.复杂地质条件下综采工作面液压支架回撤技术[J].煤炭工程,6(7):35-36.
[2]张连海,和新亮,张显峰,等.林西矿综采工作面回撤巷道支护技术实践[J].煤炭科学技术, 2009,37(5):25-26.
[3]赵俊辉.回撤通道贯通回采期顶板岩层控制研究[J].技术经验及应用,2003(5).
[4]米新民.康家滩矿88101综采面通道贯通回采期间的顶板岩层控制分析[J].山西煤炭,2005(2).
作者简介
邓新东,1975年生,大学本科学历,工程师,主要研究领域为采掘工程,现任神华宁夏煤业集团有限责任公司枣泉煤矿生产技术部副部长。