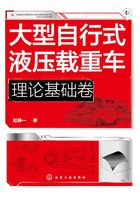
第四节 挂车结构设计及强度和刚度分析
平板车的车身结构设计要相对简单,这里对半挂车的车架结构和鹅颈结构的强度与刚度进行计算分析,以确定使用可靠。由于该车的车架和鹅颈结构比较复杂,传统的数学计算方法难以得到精确的结果,因此将采用有限元方法来对车架和鹅颈结构进行分析。
新型超长自装卸整体式运输车主要由动力升降式鹅颈、液压绞盘、中间连接平台、三轴线单元车架及过渡爬梯等结构组成,其中动力升降式鹅颈、中间连接平台、三轴线单元车架和过渡爬梯构成了该运输车的车架部。车架是组合挂车的主要承载部位,挂车所承受的载荷以及各种专用设备都直接或间接地安装在车架上,中间连接平台作为车架的主体部分,且由于其超长的尺寸,其强度及刚度特性分析是其设计过程中的关键问题。
一、整体结构设计
车架根据其结构可分为平板式、阶梯式、凹梁式(或桥式)三种结构,见图3⁃19。根据运输过程中公路对车辆高度的要求,为了保证运输车辆能顺利通过涵洞,本节采用升降式结构车架。采用此种结构可以有效地降低整车的质心高度,提高了行驶的稳定性。

图3⁃19 车架结构形式
该车特点如下:
① 车架采用可伸缩的结构。根据运输货物的长度调整车架的长度,扩大运输货物的范围。最大伸出长度为6m,伸缩后用销轴固定,该车配置了2种不同长度的管组,伸出后用长管组,完全收缩后用短管组,依次插入车架伸缩部位的两端的快速接头中。
② 货台具有可升降功能。前后部的升降分别通过前后鹅颈上的升降油缸实现。货台可由最低的地面高度升高300mm,在装卸货物时车架与地面接触,同时罐体安装在车架上可以提高车架刚度,减小变形。
③ 采用组合式可降低成本。牵引车选用大转矩的半挂牵引车牵引。半挂车由前后鹅颈、伸缩式车架和尾部悬挂车架组成,各部分为通用件,整体可在运输货物前组装,通用率高。
新型超长自装卸整体式运输车是专为城市低地板有轨电车等超长、超重货物的运输而设计制造的,图3⁃20所示为该运输车的整体结构,其主要由动力升降式鹅颈、液压绞盘、中间连接平台、三轴线单元车架及过渡爬梯等结构组成。该运输车采用了液压悬架与动力升降式鹅颈形成三点支撑,液压全轮牵引转向或液压助力转向,车架轻量化设计,具有承载能力强、载货平台高度可调、轮轴负荷均匀、装卸货物方便等优点。车辆承载平台部分安装有轨道,鹅颈部位安装有液压绞盘,可将城市低地板有轨电车通过过渡爬梯拽至车辆上方,完成有轨电车的装载。

图3⁃20 运输车整体结构
1—升降式鹅颈;2—液压绞盘;3—中间连接平台;4—三轴线单元车架;5—过渡爬梯
1.动力升降式鹅颈
图3⁃21所示为运输车动力升降式鹅颈的结构,其由牵引销、牵引转盘、牵引转向缸、加载缸、加载梁和连接端梁等组成。动力升降式鹅颈主体结构为“L”形,铰接于连接端梁,进而可与后面的承载货台连接;牵引销与牵引鞍座相连,使牵引车与半挂车连接,将牵引车的牵引力传递给半挂车;牵引转盘通过带动牵引转向缸,把牵引车的转向参数转化成液压信号,传递给后部的后端转向缸,使后端转向缸推动转向臂带动转向拉杆动作,进而推动转向轮组做出相应的转向动作;加载缸可以将悬挂液压缸的油压加载到牵引车上,实现“第五轮载荷”;鹅颈还可实现升降功能,通过加载缸的伸缩升降货台的前部以保持货台水平。

图3⁃21 动力升降式鹅颈结构
1—牵引销;2—牵引转盘;3—牵引转向缸;4,6—加载梁;5—加载缸;7—连接端梁
2.中间连接平台
该运输车的中间连接平台为“井”字形框架结构,如图3⁃22所示,由连接座总成、液压支腿、内纵梁、边纵梁、边梁、贯穿梁、滑轨及加强板组成。内纵梁和边纵梁作为连接平台的主要承载结构

图3⁃22 中间连接平台结构
1—连接座总成;2—液压支腿;3—内纵梁;4—边纵梁;5—边梁;6—贯穿梁;7—滑轨;8—加强板

图3⁃23 边纵梁箱型截面示意图
,在运输车承载行驶过程中受弯曲应力。为满足其使用性能的要求,采用Q460高强度钢制作,其中两道边纵梁采用具有很好抗弯性能的“箱型”结构,如图3⁃23所示,内纵梁采用“工”字形结构;在此基础上对三道纵梁采用预拱设计,使纵梁形状向上凸起,具有一定预拱量,可以很大程度上增大纵梁承受弯曲应力的能力,且抵消了连接平台因自重和载荷作用下的挠度,使得连接平台承载后正好处于压平状态;边纵梁的上翼面安装滑轨,两侧边梁为热轧槽钢,纵梁之间采用轻而密的贯穿梁连接,增加了整个连接平台的扭转刚度,同时还降低了与贯穿梁连接处的纵梁扭转应力;连接平台两端通过连接座分别与动力升降式鹅颈和三轴线单元车架相连接,由于连接座部位的支座反力较大,为保证该区域具有足够的承载强度,在连接座附近增加了加强板,且在一些拐角处通过采用圆弧过渡来减小局部的应力集中。
3.过渡爬梯
运输车后端的过渡爬梯用于进行货物的装卸,如图3⁃24所示,过渡爬梯分成两个模块,前模块和后模块,每个模块设有标准轨距的升降导轮和千斤顶。过渡爬梯只有在运输车装卸有轨电车时才安装,当用千斤顶将轮子降下来时,导轮与轨道变成滑动摩擦,方便爬梯在轨道上滑动,与前端三轴线单元车架拼接;装卸有轨电车时,用千斤顶将导轮升起,整个爬梯落到导轨上,使得过渡导轨工装与拖车车辆及地面轨道有良好的连接,确保有轨电车上下车时纵向车厢的折角不大于3°。

图3⁃24 过渡爬梯结构
1—前模块;2—升降导轮;3—千斤顶;4—后模块;5—导轨
二、三轴线单元模块车
如图3⁃25所示,三轴线单元模块车是由三轴线单元模块车车架、液压悬挂和转向机构组成的独立单元模块。车架由箱型结构的主梁以及若干横梁和支撑梁焊接组成,为空间框架式结构,具有足够的承载强度和刚度。车架前后为端横梁,供与中间连接平台连接或安装操纵箱。车架横梁端部有紧固货物用的拉环及安装液压悬架管路的高压截止阀、安全阀,大梁腹部的矩形口供布置转向杆系用,大梁两侧用于装设液压、制动管路。液压悬挂如图3⁃26所示,主要由旋转立轴、悬臂、悬挂柱塞缸和平衡臂等部件组成,主要起到支撑货物和升降货台高度的作用。悬臂通过一组平面止推滚动轴承及两只滑动球关节轴承与悬挂立轴相连,承受分配到悬挂上的载荷,并在转向拉杆牵引下能使轮轴灵活地旋转一定角度,当悬挂与转向杆系脱开时,该轮轴随同悬挂可作360°回转,便于轮轴、轮胎的拆装维修。转向机构主要由转向支架、转向臂、转向拉杆和转向液压缸组成,主要起到转向时推动各转向轮按要求进行转向的作用。

图3⁃25 三轴线单元模块车结构组成
1—三轴线单元模块车车架;2—液压悬挂;3—转向机构

图3⁃26 液压悬挂结构
1—悬臂;2—悬挂柱塞缸;3—旋转立轴;4—螺栓;5—平衡臂
三、连接平台强度和刚度分析及预拱设计
目前,国内外常见的轴线单元模块及其拼车连接结构都已经标准化,承载连接平台的拼车连接结构也与之相适应。为了提高组合挂车的承载能力,在拼车结构不变的情况下,国内目前主要是采用高强度的材料和轻量化的方法。而在新型超长自装卸整体式运输车的结构设计过程中,在采用高强度材料及轻量化的基础上,通过对连接平台纵梁采用预拱设计,使连接平台具有一定的预拱量来提高连接平台的承载能力,以抵消连接平台中心在自重及载荷作用下产生的挠度。增大运输车运输过程中的安全性和可靠性。
预拱量是为抵消梁、拱、桁架等结构在载荷作用下产生的挠度,而在制造时所预留的与位移方向相反的校正量。具有一定预拱量的结构密度小、跨度大,并且可以充分利用材料的强度,在全跨载荷作用下具有承载力强、变形小的优点。
新型超长自装卸整体式运输车的承载能力是由动力升降式鹅颈、三轴线单元车架、中间连接平台及其与单元模块车和动力升降式鹅颈的拼车连接结构的承载能力共同决定的。由于运输车具有超长连接平台及车体长度的特点,而连接平台作为主要的承载平台,其结构强度和刚度的大小直接决定了运输车承载能力的大小。因此,下面通过对未采用预拱设计的连接平台和采用预拱设计的连接平台进行强度和刚度对比分析,就连接平台纵梁采用预拱设计对提高运输车在运输货物过程中的抗弯能力及承载能力进行说明。
1.有限元建模及网格划分
通过三维绘图软件Pro/Engineer对未采用预拱设计的连接平台进行三维实体建模,如图3⁃27所示,并通过ANSYS Workbench与Pro/Engineer的数据交换接口将三维实体模型导入ANSYS Workbench中。在不影响连接平台主要力学特性和分析精度的前提下,对连接平台的三维实体模型进行了以下简化:

图3⁃27 连接平台三维实体模型
① 省略非承载部件和一些对连接平台刚度及强度影响不大的结构。如液压支脚连接板和固定板,其不起支撑作用,且对连接平台的强度大小并没有影响。
② 简化一些影响不大的小孔。如管路固定板上的孔,用于固定液压管路,对连接平台的强度大小影响不大。
选择连接平台的材料为钢结构材料,并对导入后的几何模型进行检查及几何清理,消除不必要的细节特征,提高网格的划分质量和速度,从而提高计算精度。有限元分析模型的准确程度以及模型规模是否合适,对连接平台结构的分析至关重要。图3⁃28所示为连接平台的网格划分图,完成网格划分后的连接平台被划分为193597个节点,92261个实体单元。

图3⁃28 连接平台网格图
2.约束及载荷的确定
有轨电车的重量通过车轮与运输车边纵梁上的导轨接触将载荷作用在平台的导轨上,连接平台通过两端的连接座分别与动力升降式鹅颈和三轴线单元模块车的连接座以销轴连接固定,连接座下端有连接销孔和连接销座,平台所受载荷通过两端的连接座传递给动力升降式鹅颈和三轴线单元模块车。
运输车的设计载荷为55t,实际装载50t,但作用在连接平台上的载荷为35t,其余15t载荷直接作用在三轴线单元模块车上。由于只对连接平台的强度和刚度进行分析,不考虑三轴线模块单元,因此只对连接平台施加35t的载荷。
进行有限元强度及刚度分析时,对连接平台两端的连接座销轴孔分别施加圆柱面约束,限制其轴向和径向两个方向的自由度,切向方向设置为自由状态,模拟圆柱销对连接平台的约束作用。对连接平台的导轨分别施加20t和15t的跨距载荷作用,模拟有轨电车车轮对导轨的载荷作用,同时添加连接平台自身的重力作用。连接平台的约束及载荷情况如图3⁃29所示。

图3⁃29 连接平台的约束及载荷
3.强度和刚度分析及预拱设计
由于约束部分与实际支撑存在一定差距,导致约束周边的应力不真实,且这里的主要研究目的为纵梁及贯穿梁部分的强度及弯曲刚度,则在进行连接平台形变位移和应力分布求解时,不考虑约束周边的结构。
考虑一定的安全系数,则连接平台的许用应力[σ]可按下述公式计算:
[σ]=(3⁃5)
式中 σs——连接平台的屈服强度,MPa;
n——安全系数。
新型超长自装卸整体式运输车连接平台的纵梁采用Q460高强度钢制作,屈服强度σs=460MPa,边梁和贯穿梁采用16Mn,屈服强度σs=350MPa,取安全系数n=1.4;将参数取值代入公式(3⁃5)计算可得连接平台纵梁的许用应力[σ]=329MPa,边梁和贯穿梁的许用应力[σ]=257MPa。
由于连接平台超长的尺寸,还应考虑其挠度,连接平台纵梁的弯曲变形,取决于纵梁的刚度,在静载情况下,允许纵梁的最大变形量为:
ymax=(0.002~0.003)L(3⁃6)
式中 ymax——纵梁的最大变形量,m;
L——连接平台的跨距,m。
连接平台跨距为24780mm,则可得纵梁最大变形量为ymax=74.34mm。
完成约束与载荷的施加后,对未采用预拱设计的连接平台的形变位移及应力分布进行求解,可得其位移图解如图3⁃30所示,应力图解如图3⁃31所示。

图3⁃30 未采用预拱设计的连接平台位移图解

图3⁃31 未采用预拱设计的连接平台应力图解
由以上求解结果可知,在载荷及自身重力的静态作用下,未采用预拱设计的连接平台的最大形变位移发生在中间位置,为102.43mm,远远超过其最大变形量的允许值;最大应力发生在靠近端部的加强板部位,如图3⁃32所示,为238.35MPa,小于其许用应力值。连接平台的强度满足规定要求,但是纵梁的最大变形量却不满足要求,说明纵梁的弯曲刚度不足,针对如此情况,不改变纵梁的制作材料,对纵梁采用预拱设计,使纵梁具有一个向上的预拱量,以抵消其在承载时的挠度。

图3⁃32 未采用预拱设计的连接平台最大应力部位
根据上述有限元求解结果,未采用预拱设计的连接平台在载荷及自重作用下的形变位移为102.43mm,则对纵梁采用预拱设计,预拱量为110mm,在相同约束及载荷条件下,对具有110mm预拱量的连接平台进行有限元分析求解,可得其位移图解如图3⁃33所示,应力图解如图3⁃34所示。

图3⁃33 具有110mm预拱量的连接平台位移图解

图3⁃34 具有110mm预拱量的连接平台应力图解
由以上求解结果可知,在载荷及自身重力的静态作用下,具有110mm预拱量的连接平台的最大形变位移发生在中间位置,为72.232mm,被110mm的预拱量抵消后依然具有37.768mm的上拱量;最大应力也发生在加强板部位,如图3⁃35所示,为218.46MPa,小于其许用应力值。

图3⁃35 具有110mm预拱量的连接平台最大应力部位
通过对比分析未采用预拱设计的连接平台与具有110mm预拱量的连接平台的位移图解和应力图解可知,采用高强度钢材料的连接平台满足运输车承载的强度要求,但是在不采用预拱设计的情况下,纵梁的弯曲刚度不满足要求,在自重及载荷作用下中间位置的弯曲变形量太大。为增大纵梁的弯曲刚度,减小其中间位置的挠度,对纵梁采用了预拱设计。对纵梁采用110mm的预拱量设计后,在相同约束和承载条件下,相比未采用预拱设计的情况,连接平台的最大形变位移明显减小,且经预拱量抵消后依然具有少许上拱,使得连接平台在自重及载荷作用下接近压平状态而不会下弯,最大应力值也有所减小,使得连接平台的强度和刚度均明显增大,从而满足规定要求。由此可得,采用预拱设计可以提高连接平台的弯曲刚度,减小其最大挠度,使得运输车装载后正好可将车架压平而不下弯,同时还可以改善连接平台的应力分布,增大了连接平台的承载能力,从而使运输车在运输过程中具有更高的安全性和可靠性。
小结:本章对新型超长自装卸整体式运输车的整体结构设计进行了介绍,通过三维绘图软件Pro/Engineer建立了中间连接平台的三维实体模型,并将其导入ANSYS Workbench中。根据运输车实际运输过程中的约束及载荷情况,建立了连接平台的有限元模型,求解得到未采用预拱设计的连接平台的形变位移及应力分布,根据求解结果对连接平台采用了预拱设计;然后对比分析了两种不同设计结构下的有限元求解结果,说明对连接平台采用预拱设计可以增大其弯曲刚度和强度,提高整车的承载能力,进而保证了运输车运输过程中的安全性和可靠性。