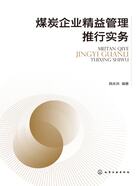
3. 中国推行精益生产方式
从计划经济时代开始,中国的企业一直在探讨提升企业运营效率的方式,例如“鞍钢宪法”等,当中国汽车行业于20世纪70年代初开始与日本汽车企业合作以后,中国对精益生产方式的学习就开始从被动模仿进入到主动探索阶段。
【阅读材料0-2】中国企业学习、探索精益生产方式的过程
①1978年6月第一汽车制造厂组建一汽考察团访日,正式拉开了中国学习丰田模式的“纪元”,一汽向丰田提出对第一汽车制造厂进行“工厂诊断”的请求。同年11月,日本的丰田第一汽车调查团访华。调查团主要针对一汽解放卡车生产线进行了细致的诊断,为一汽生产管理者提出了许多“颠覆性”的建议。第一汽车制造厂变速箱分厂成了中国制造业学习丰田生产模式的第一个“样本”工厂。
②1981年,丰田精益生产“宗师”大野耐一访问一汽。面对生产管理中明显的浪费,他一边在现场帮助进行改善指导,一边开展讲座,并通过建造两条模范生产线,将精益生产的理念全面向一汽其他工厂推广。随后,丰田还在南京汽车厂和西安交大等地举办精益生产模式讲座。
③随着1984年丰田集团大发公司开始向天津汽车的华利提供技术援助并转让夏利轿车生产,精益生产开始在天津扎根。丰田生产模式随着丰田在华的合作而在中国得到传播。
④1988—1989年,在沈阳建立中国汽车工业丰田金杯技工培训中心,并同时向金杯客车进行技术转让。丰田下功夫“辅导”的沈阳金杯客车公司,将精益生产理念传承下来。
⑤1990年开始,丰田在天津开始设立众多零部件企业,打造未来合资的生产基础。中国的精益生产学习重镇开始转移到天津,天津丰田发动机有限公司甚至在中国工业工程圈子里被公认为学习精益生产的优等生。
⑥1998年丰田与四川旅行车制造厂合资成立了四川丰田。通过精益生产模式的改造,无论是业绩还是管理,四川丰田已经成为丰田的中国范本。
⑦2000年后,中国汽车市场进入竞争时代。但随着生产规模的提升,质量的不稳定越来越突出,尤其是在合资生产中接触了德国、美国、法国等不同的生产管理模式,中国汽车制造商开始深刻认识到精益生产在质量控制方面的优势。
⑧2002年,一汽集团成立丰田生产方式领导小组。当年9月,一汽轿车公司由20多个车间领导和生产骨干组成考察组,花费一个多月时间去日本学习丰田精益生产。随后,在激烈的市场竞争和巨大生产过剩压力下,“向丰田学习”的理念也从汽车工业向中国整个制造业展开,无论国有企业、民营企业还是外资企业,都期望通过精益生产降低浪费、提高效益,中国的精益生产学习从被动模仿进入了主动探索阶段。
实际上,随着社会经济与消费方式的演进,以及技术的不断进步,丰田精益生产方式在中国的推进、发展经历了三个阶段。
第一阶段是基于降低成本、提高品质的目的来学习、模仿丰田精益生产方式。如何消除精益所强调的7种浪费,如何通过大野耐一圈找到现场浪费点,然后不断改善。企业要想降低成本,首先必须有质量意识,质量作为客户的根本需求必须优先考虑,成本是质量活动的结果,但中国企业最先考虑的还是成本,通过各种方式来降低成本。这个阶段最主要的特征是项目的效果多数以成本节省来衡量。
第二个阶段是基于缩短交付周期(交期)的目的学习、模仿丰田精益生产方式。精益的本质并不是降低成本,而是基于时间的竞争。大野耐一说过,“所有我们做的,就是不断压缩从客户下单那一刻起,直到我们收到货款所用的时间。我们通过减少无附加价值的浪费,缩短时间”。以工业仪器及设备为主要业务的跨国企业丹纳赫的CEO说过,“你想降低成本可以,不管用老掉牙的方法,还是用精益的方法,那也是新瓶装旧酒,精益的本质是压缩时间”。这就是企业生产与运营的时间价值,所以企业需要考虑自己的流动性,缩短周期(包括生产周期、投资周期、库存周期等)。
第三个阶段是基于以客户价值为导向的精益改善阶段。为了生存,企业需要不断为客户创造价值。例如,新能源汽车、无人驾驶技术的发展推动汽车行业重新洗牌;再比如,数码技术的兴起使柯达破产,智能手机的崛起使尼康中国工厂关闭,这都是客户价值出了问题所导致的失败。企业的价值定义错了,一切改善都是浪费,所以需要首先定义客户价值。客户价值包括产品的独特特征给客户传递独特价值,价值传递过程中的独特特征、额外的服务等。从客户价值出发寻找改善的方向与重点,这就是目前国内企业所处的精益发展与完善的阶段。