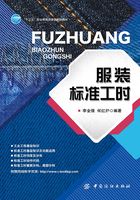
第六节 动作改善
动作改善的步骤,如果用PDCA的方法进行分析的话,遵循这样的步骤进行动作分析改善,可以使动作的效率不断得到提升。
动作分析改善的步骤:
一、发现问题
生产制造的现场,每天都有新的问题在发生。有些人可能视若无睹,觉得一切都很正常,因而也就缺少改善的动因,效率也就日复一日地停留在同一水平上。改善往往源于问题的发生和发现,管理者如果能带着疑问审视现场所发生的一切,特别对细节的地方加以留意,就更容易找到改善的对象。
二、现状分析
问题发现以后,就应该针对问题发生的现场,展开细致的调查,掌握数据,进行录像拍摄,使问题进一步明确。然后根据掌握的事实,展开分析。这个步骤中,应坚持以下原则(表1-6):
表1-6 现状分析

三、找出问题的原因
通过现状的分析以后,可以得到一些问题的可能原因。这时,应该逐一加以验证,把一些似是而非的原因排除掉,找到真正导致问题的原因。排除的过程应该坚持先简单后复杂,先成本低后成本高的原则。
四、拟定改善方案
原因找到之后,就应该拟定改善方案,可参考图1-4改善有效动作、减少辅助动作、消除无效动作。
帮助拟定改善方案。
改善方案拟定之后,应该与相关人员检查其中是否有缺失遗漏,进一步使之完善,避免产生负作用(图1-5)。

图1-4 动作分解记号化

图1-5 动作分解图表
五、改善方案的实施
改善方案确定以后,就该集中相关人员进行说明训练,将任务分派下去,并对改善过程进行追踪监控。一旦有不理想的地方,还应及时进行调整。
六、改善效果确认
改善方案实施完成后,应收集各方面数据,与改善之前的数据进行比较,请参考图1-6、图1-7,确认改善是否达成了预想的目标。由于生产现场的目标离不开PQCDSM(效率、品质、成本、交期、安全、士气)几个方面,所以以下数据收集比较也就顺理成章了。
产量、移动率、能率、作业时间、不良率、合格率、客户抱怨件数、材料损耗率、人工成本、间接人员比例、按时交货率、平均延误天数、安全事故件数、安全检查结果、违纪个件数、改善提案件数、员工离职率、员工抱怨件数。
七、标准化
倘若效果较为明显,就应通过标准化加以维持。确定本公司的标准工时及标准方法,制订新的作业标准书、现场整理布置规范、安全操作规程、工程巡视要点等文件并正式发布实施,这样也就完成了一个工作改善的循环。

图1-6 动作分解对比

图1-7 动作分解图表数据对比